July 04, 2025
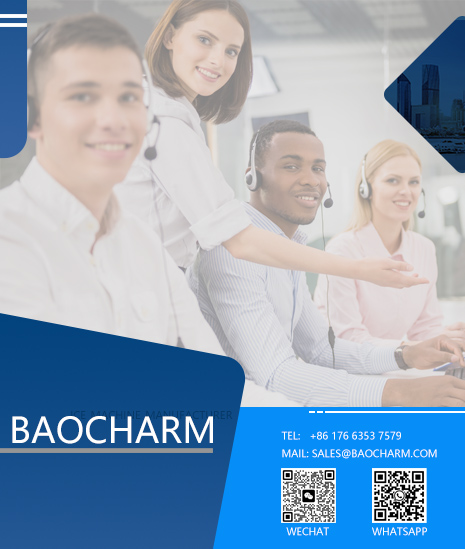
We are the industry-leading manufacturer of ice machine china, pull back the curtain to give you an exclusive look into the inner workings of our Quality Assurance (QA) department. In this detailed exploration, we aim to showcase the meticulous processes we employ to ensure that every piece of ice maker machine we manufacture meets the highest standards of quality. Today, we invite you to join us on a virtual tour through the various stages of quality control that take place before our block ice maker machine 20 ton is shipped to our valued customers.
The journey of quality assurance begins with the incoming material inspection. This critical step is where we verify that all components and raw materials meet our stringent specifications. Our QA team meticulously inspects each batch for any signs of defects or discrepancies. The criteria for acceptance are strict, and only materials that pass our tests are allowed to proceed to the production floor.
As the production process unfolds, our QA department conducts regular and systematic inspections of the components being manufactured. This involves a thorough examination of each part at various stages of assembly. The purpose of these production line inspections is to catch any potential issues early on, ensuring that each component is up to standard before it is integrated into the final product.
The inspections include, but are not limited to, the following:
Once the equipment is fully assembled, it undergoes a comprehensive final inspection. This is where our QA team leaves no stone unturned, examining every aspect of the equipment to ensure it is ready for use. The final inspection includes several critical checks:
The final stage before our equipment is shipped is a thorough testing and adjustment phase. This is where we simulate real-world operating conditions to ensure that every piece of equipment not only meets but exceeds performance expectations. The testing phase includes:
Quality is not just a promise at our company; it’s a commitment that we live by every day. Our Quality Assurance department is the backbone of this promise, working tirelessly to ensure that every product we deliver is of the highest caliber. Whether it's a mini ice plant machine, or a large scale ice machine, our QA processes are designed to deliver reliability, performance, and satisfaction to our customers.
We hope this insight into our QA department has given you a greater appreciation for the care and dedication that goes into every piece of good quality ice machine we produce. Stay tuned for more technical insights from our team, and thank you for joining us on this tour of quality assurance at its finest.
Our Contacts
Email: sales@baocharm.com
WhatsApp: +852 5510 1036
Wechat: +86 17663537579
Working Hours: Mon ~ Sat 8:30 AM - 5:30 PM